MEMS, technology and its MEMS inertia technology introduction
Release time:
2025-07-07
In today's interconnected and intelligent era, a' micro giant' technology is quietly driving the precise perception and intelligent decision-making of countless devices —— This is MEMS (Micro-Electro-Mechanical Systems) technology and its core branch, MEMS inertial technology. Despite their tiny size, these technologies are reshaping our understanding of motion, posture, and position.
MEMS technology: precision engineering in the microscopic world
MEMS, or Micro-Electro-Mechanical Systems, is a complex system that integrates microelectronics and micro-mechanics. It combines mechanical structures, electronic components, sensors, and actuators on a scale of 1 to 100 micrometers. The core technology involves using advanced semiconductor manufacturing processes, such as lithography, etching, and thin film deposition, to mass-produce movable micro-mechanical devices on substrates like silicon wafers.
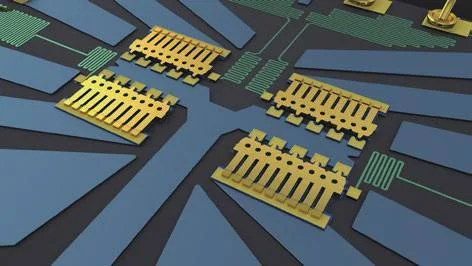
technical feature
· Miniaturization: Small size, significant space and energy savings.
· Integration: The mechanical structure and signal processing circuit can be integrated on a single chip to improve performance and reliability.
· Mass production: along with semiconductor process, low cost and good consistency.
· Multifunctionality: can realize sensing (such as pressure, acceleration, chemistry), execution (such as micro-mirror, inkjet head), energy harvesting and other functions.
application area
· Consumer electronics: Smart phones (accelerometer, gyroscope, microphone, pressure sensor), game controllers, wearable devices.
· Automotive industry: airbag collision sensors, tire pressure monitoring, engine management pressure sensors, electronic stability program.
· Medical health: drug delivery micropumps, miniature pressure sensors, portable diagnostic equipment.
· Industrial Internet of Things: Equipment status monitoring, process control sensors.
In addition, MEMS technology is also playing an important role in aerospace, industrial automation, environmental monitoring and other fields.
MEMS inertial technology: the core of motion sensing
MEMS inertial technology is one of the most successful and widely used branches in the MEMS field, focusing on measuring the motion state (acceleration, angular velocity) and spatial attitude (tilt, heading) of objects
Core components:
1. MEMS accelerometer:
o Function: Measure the linear acceleration (a) and gravity acceleration (g) of an object.
o Principle: The core is a movable "mass-block-spring" microstructure. When subjected to acceleration, the inertial force causes the mass block to shift (most commonly through changes in capacitance), which is then converted into an electrical signal by the detection circuit. By measuring the gravitational component, the angle of inclination of the object relative to the horizontal plane can also be calculated.
o Applications: automatic rotation of mobile phone screen, pedometer, car collision detection (airbag), hard disk drop protection, device posture monitoring.
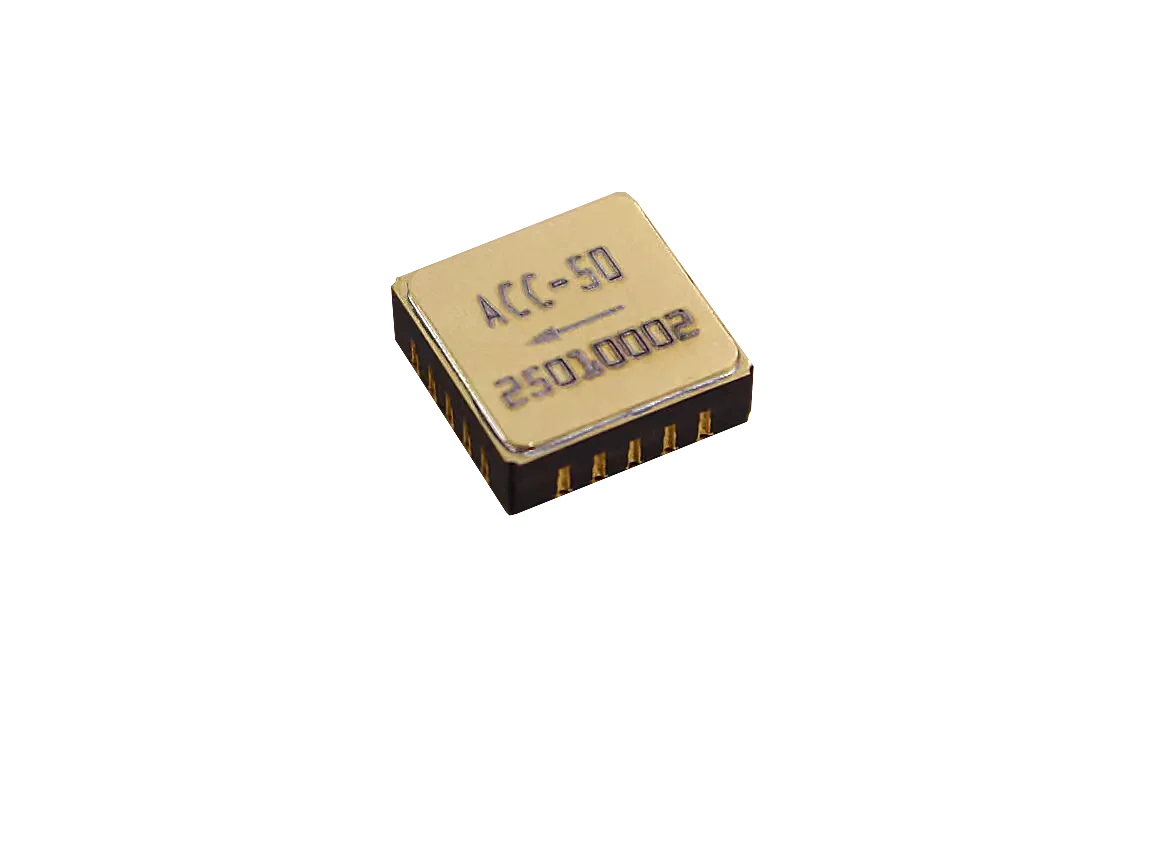
2. MEMS gyroscope :
o Function: Measure the angular velocity (ω) of an object rotating around an axis.
o Principle: The Coriolis force is used. It usually consists of a mass block that vibrates at high speed (driving mode). When the device rotates around an axis perpendicular to the vibration direction, the Coriolis force causes the mass block to shift in another perpendicular direction (detection mode). This displacement is detected and converted into an angular velocity signal.
o Applications: anti-shake for mobile phone, camera and UAV, motion sensing control for games, car navigation (change of heading Angle), and robot posture stabilization.
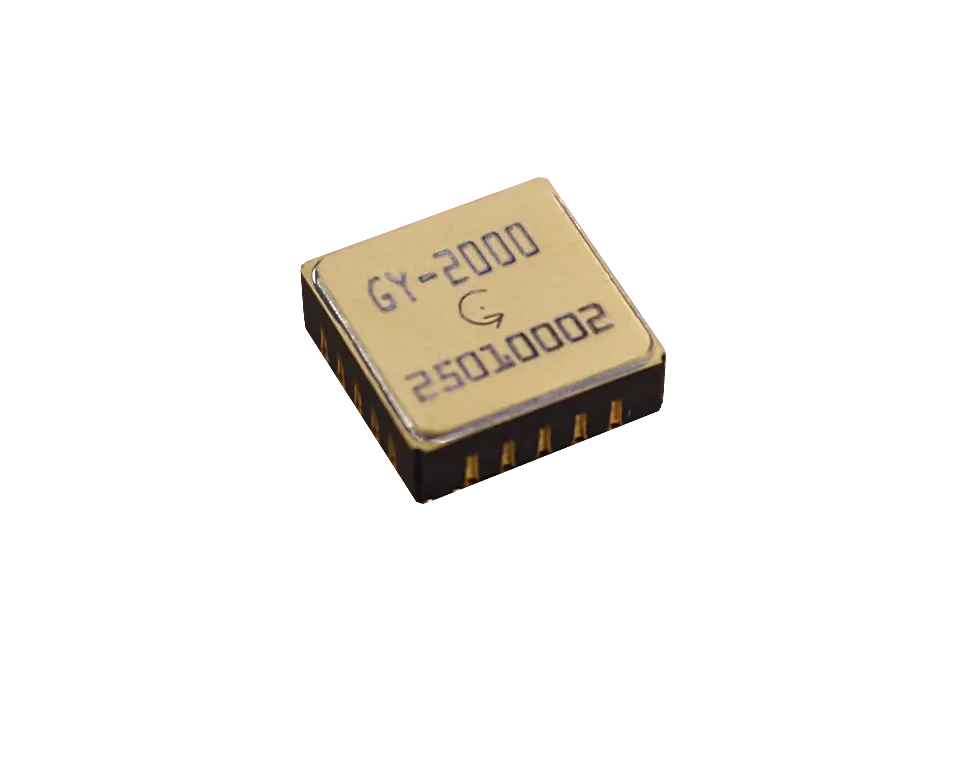
3. MEMS inertial measurement unit:
o Function: Multiple MEMS inertial sensors (usually 3-axis accelerometer + 3-axis gyroscope) are integrated into a single package, sometimes with a magnetometer (electronic compass) and processor. Provides more comprehensive motion information (three-axis acceleration, three-axis angular velocity).
o Advantages: small space occupancy, low cost, high alignment accuracy of each axis, simplified system design.
o Core task: Through the inertial navigation algorithm (attitude calculation, course prediction), multi-sensor data is fused to estimate the three-dimensional attitude, velocity and position of the object in real time (drift error will accumulate with time, which needs the assistance of other sensors, such as GNSS, magnetometer and vision).
o Applications: UAV/Autonomous vehicle navigation and control, smartphone/AR/VR motion tracking, robot autonomous navigation, platform stabilization system, pedestrian position prediction.
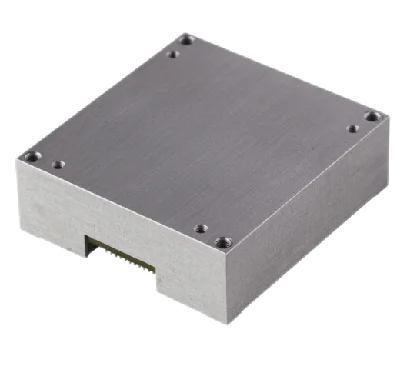
Advantages and challenges of MEMS inertial technology
superiority :
· Small size, light weight: easy to embed in a variety of portable and space limited devices.
· Low power consumption: Suitable for battery-powered mobile and Internet of Things devices.
· Low cost: the advantage of mass production is significant.
· High reliability: solid state structure, no moving parts wear (compared with traditional mechanical gyroscope).
· Start fast: no warm-up time required.
throw down the gauntlet :
· Accuracy limit (especially for low-end devices): There are zero bias (Bias), scale factor error, nonlinearity, noise, etc., which lead to the accumulated position error (drift) over time. The cost of high-precision MEMS (such as tactical level and navigation level) increases significantly.
· Temperature sensitivity: The performance is easily affected by temperature changes and requires temperature compensation.
· Vibration sensitivity: Vibration at a specific frequency may interfere with the measurement.
· Calibration requirements: Calibration is usually required at the factory and during use to compensate for errors.
Fourth, application field outlook
MEMS inertial technology has been deeply integrated into modern life and industry:
· Consumer electronics: Smart phones, tablets, wearables, game consoles, camera stabilization.
· Automotive electronics: Electronic stability system, airbags, navigation, ADAS, autonomous driving.
· Industry and energy: Platform stability, mechanical health monitoring, robotics, precision agriculture.
· Drones and robots: flight control, autonomous navigation, attitude stability.
· Emerging fields: AR/VR motion tracking, indoor positioning, medical device navigation, Internet of Things perception.
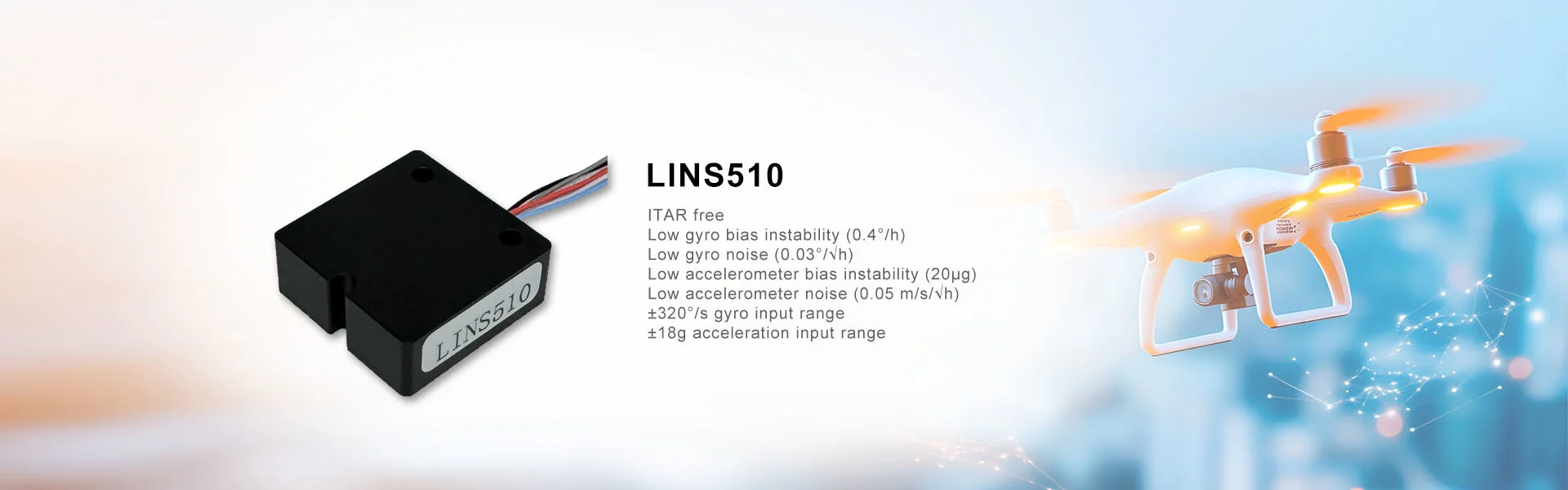
V. Future development trends
· Continuous improvement of performance: new materials, new structures, and new detection mechanisms (such as optical MEMS) are pursued for higher accuracy, lower noise, and better stability.
· Multi-sensor deep fusion: IMU is deeply integrated with GNSS, magnetometer, barometer and visual/lidar to achieve more robust and accurate positioning and navigation.
· Higher integration: sensors, processors, algorithms and even wireless communications are integrated into a single chip or package (such as smart sensors).
· Driven by emerging applications: the demand for high-performance and low-cost MEMS inertial devices is surging due to autonomous driving, UAV logistics, metaverse, micro-robots, etc.
· Artificial intelligence empowerment: Use AI algorithms for more intelligent sensor error modeling, compensation and motion pattern recognition.
epilogue
MEMS technology, particularly MEMS inertial technology, acts as the 'micro-perception organs' that perceive the mysteries of physical world movements. With their revolutionary advantages of miniaturization, low cost, and high integration, these technologies are found everywhere—from the compact smartphones to the soaring drones and the self-driving cars exploring the unknown—silently supporting the underlying perception needs of the intelligent wave. As technology continues to evolve and multidisciplinary integration progresses, MEMS inertial technology will undoubtedly play an increasingly crucial role in building a smarter, more interconnected, and more automated future world. The power of this 'micro-dust' is shaking the entire tech world.
Company News